Si eu m-am intrebat cum functioneaza celelalte automobile fara MAF. Ideea e ca au alt senzor: "MAP". Sunt curios care sunt avantajele si dezavantajele celor 2 sisteme de masura..
"A manifold absolute pressure sensor (MAP) is one of the sensors used in an internal combustion engine's electronic control system. Engines that use a MAP sensor are typically fuel injected. The manifold absolute pressure sensor provides instantaneous manifold pressure information to the engine's electronic control unit (ECU). This is necessary to calculate air density and determine the engine's air mass flow rate, which in turn is used to calculate the appropriate fuel flow. (See stoichiometry.)
An engine control system that uses manifold absolute pressure to calculate air mass uses the speed-density method. Engine speed (RPM) and air temperature are also necessary to complete the speed-density calculation. Not all fuel-injected engines use a MAP sensor to infer mass air flow; some use a MAF (mass air flow) sensor. Several makes use the MAP sensor in OBD II applications to test the EGR valve for functionality. Most notably General Motors uses this approach."
MAF vs MAP :
"For: Map lets you have no sensor diameter restriction before the turbo
Against: A Q45 AFM is as big as most turbo inlets anyway
For: MAP is 'immune' to air leaks in the intercooler system
Against: Air leaks are easier to diagnose with an AFM
For: MAP enables better resolution tuning
Against: AFM is more acceptable to changes in engine modifications - if you add a bigger exhaust for example, and have a MAP you have to retune, AFM will compensate.
For: MAP sensor equipped standalones give greater control over tuning
Against: Factory ECU does auxillary tasks like cold start, air con, damage prevention a whole lot better than standalone will (without heaps of tuning and dyno time)
For: Standalone comes with software and hardware interfaces that let you do things like data logging and super fine tuning and nerdy stuff like rotational idle, antilag, launch control.
Against: Developments in addons for the factory ecus are enabling real time tuning, data logging, launch control, rotational idle, antilag, turbo timers, security etc. "
Last edit:
"Once upon a time an engine needed three things to run: fuel, air, and fire. That’s what carbs, coils, and distributors are for. Modern EFI engines still need these three elements, but they use different hardware to provide them, and a computer to run the whole process.
Today’s electronic engine management systems can process millions of instructions per second to continuously adjust spark and fuel for optimum performance. The computer regulates the electronic fuel-injector pulse width (the time that the fuel injector is open) and ignition lead with input from various sensors. One of the key things the computer needs to know is how much air the engine consumes under a given set of conditions. Three different measurement strategies have evolved to supply the computer with this basic information; in order of sophistication they are: N Alpha, Speed Density, and Mass Flow metering.
N Alpha
A relatively simple design, N Alpha systems use only engine speed and throttle angle to calculate the amount of fuel needed by the engine. This system doesn’t measure airflow directly; instead, engine load is assumed based on throttle-angle versus engine rpm. The various load-rpm points make up the computer’s lookup table, with the amount of fuel needed at each point manually programmed by the tuner. N Alpha systems work well on engines that operate primarily at wide-open throttle—such as race cars—but are much less accurate at part-throttle than more sophisticated systems because of their relatively simple fuel map. They generally do not have a closed-loop mode for air/fuel correction, resulting in part-throttle calibration that is crude at best when compared to other systems. This also makes them incompatible with modern catalytic converters. Any significant engine change requires remapping.
Speed Density
Speed Density systems accept input from sensors that measure engine speed (in rpm) and load (manifold vacuum in kPa), then the computer calculates airflow requirements by referring to a much larger (in comparison to an N Alpha system) preprogrammed lookup table, a map of thousands of values that equates to the engine’s volumetric efficiency (VE) under varying conditions of throttle position and engine speed. Engine rpm is provided via a tach signal, while vacuum is transmitted via an intake manifold-mounted Manifold Air Pressure (MAP) sensor. Since air density changes with air temperature, an intake manifold-mounted sensor is also used.
Production-based Speed Density computers also utilize an oxygen (O2) sensor mounted in the exhaust tract. The computer looks at the air/fuel ratio from the O2 sensor and corrects the fuel delivery for any errors. This helps compensate for wear and tear and production variables. Other sensors on a typical Speed Density system usually include an idle-air control motor to help regulate idle speed, a throttle-position sensor that transmits the percentage of throttle opening, a coolant-temperature sensor, and a knock sensor as a final fail-safe that hears detonation so the computer can retard timing as needed.
GM’s Tuned Port Injection (TPI) set-ups used Speed Density metering from ’90-’92, as did ’91-’93 LT1 engines. All ’86-’87 and ’88 non-California Ford 5.0L-HO engines used Speed Density metering. Most Mopar fuel- injection systems have used Speed Density too.
Because a Speed Density system still has no sensors that directly measure engine airflow, all the fuel mapping points must be preprogrammed, so any significant change to the engine that alters its VE requires reprogramming the computer.
Mass Flow
By contrast, Mass Air Flow (MAF) systems use a sensor mounted in front of the throttle body that directly measures the amount of air inducted into the engine. The most common type of mass-flow sensor is the hot wire design: Air flows past a heated wire that’s part of a circuit that measures electrical current. Current flowing through the wire heats it to a temperature that is always held above the inlet air temperature by a fixed amount. Air flowing across the wire draws away some of the heat, so an increase in current flow is required to maintain its fixed temperature. The amount of current needed to heat the wire is proportional to the mass of air flowing across the wire. The mass-air meter also includes a temperature sensor that provides a correction for intake air temperature so the output signal is not affected by it.
The MAF sensor’s circuitry converts the current reading into a voltage signal for the computer, which in turn equates the voltage value to mass flow. Typical MAF systems also use additional sensors similar to those found in Speed Density systems. Once the electronic control module (ECM) knows the amount of air entering the engine, it looks at these other sensors to determine the engine’s current state of operation (idle, acceleration, cruise, deceleration, operating temperature, and so on), then refers to an electronic map to find the appropriate air/fuel ratio and select the fuel-injector pulse width required to match the input signals.
GM used MAF sensors on the turbo Buick V-6 Grand National, ’85-’89 TPI, ’94-’98 LT1, ’96 LT4, and all LS1 engines. Ford has used MAF metering on ’88 California 5.0L engines and all ’89-and-later V-8 engines.
MAF systems are much more flexible in their ability to compensate for engine changes since they actually measure airflow instead of computing it based on preprogrammed assumptions. They are self-compensating for most reasonable upgrades, as well as extremely accurate under low-speed, part-throttle operation. On the other hand, the MAF meter, mounted as it is ahead of the throttle-body, can become an airflow restriction on high-horsepower engines. On nonstock engine retrofits or EFI conversions on engines never produced with fuel injection, it may be hard to package an MAF meter within the confines of the engine bay and available intake manifolding.
Which Is Best?
In a perfect world, virtually all street-performance engines would use Mass Air, due to its superior accuracy and greater tolerance for engine changes. In the past there was a problem on high-horsepower engines because larger-capacity MAF sensors were scarce and prohibitively expensive. Nowadays, oversize MAF sensors are available from Pro-M, Granatelli Racing, and other sources that are compatible with Ford engines and computers. Custom MAF calibration keyed to the specific vehicle, engine, and injector size is also available. With a correctly calibrated oversize meter, reflashing the Ford computer usually isn’t required. (However, before you run out for a larger Ford MAF meter, Fast Track Performance points out that the first limiting factors are the puny Ford 19 lb/hr injectors, which can only support about 320 hp.)
Some oversize MAF meters have also become available for the second-generation (’94-and-later) GM MAF systems, but the selection isn’t as broad as for the Ford guys. The GM MAF engine management computer isn’t as adaptable as Ford’s. Although it will accept larger MAFs, you can’t go up and down more than one injector size with reflashing the computer.
Bigger MAF meters are not readily available for old GM TPI systems, but Granatelli says it is possible to adapt Ford meters to them via a conversion wiring harness. Custom calibration is required, so Granatelli prefers to do the changeover in-house.
For radical engines or engines never produced with fuel injection, an aftermarket user-programmable computer system is usually preferred. Unfortunately, the more-or-less affordable aftermarket systems—including ACCEL/ DFI, Speed-Pro, and Holley—are Speed Density–based and don’t support Mass Air metering. Those systems that do—including Electromotive, Motec, and Pectel units—are more costly, sometimes considerably so. However, Westech Performance reports that it is possible to use Pro-M’s adjustable Optimizer MAF meter and a stock Ford Mustang computer with Ford’s EPEC piggyback programmable unit to run Mass Air on any engine.
If it is not practical to use MAF on your engine due to packaging or hardware constraints, the programmable Speed Density systems are the next best choice because production-based Speed Density systems won’t tolerate major engine changes without computer reprogramming, which usually requires the services of an outside specialist; if the reprogrammer isn’t specifically familiar with your combo, the end results may be less than satisfactory.
On radical engines (those with cam duration over 240 degrees at 0.050 or less than 10 inches of idle vacuum), even user-programmable Speed Density systems have difficulty due to an erratic or insufficient manifold vacuum signal. If the application is for a race car operated primarily under full throttle, N Alpha is the solution. If you intend to drive on the street, a system that blends N Alpha with Speed Density—varying which is in control per specific operating point and conditions—may be the answer. The higher-end aftermarket systems, including Electromotive’s, support this option.
As electronic engine-management system usage becomes more widespread in the car crafting community, prices and ease of use should become more user-friendly. Already, the latest Gen VII ACCEL/DFI system has the ability to construct its own baseline fuel curve, and the new user programming interface is a full-fledged, Windows-compatible program. Can voice command be far behind?"
Attachments: |
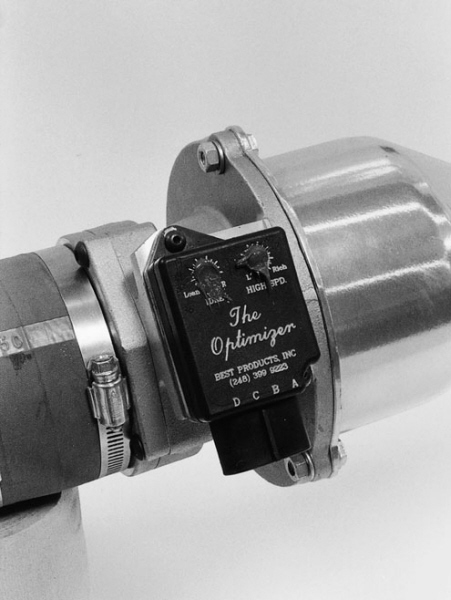
p76771_image_large.jpg [ 88.09 KiB | Viewed 6096 times ]
|
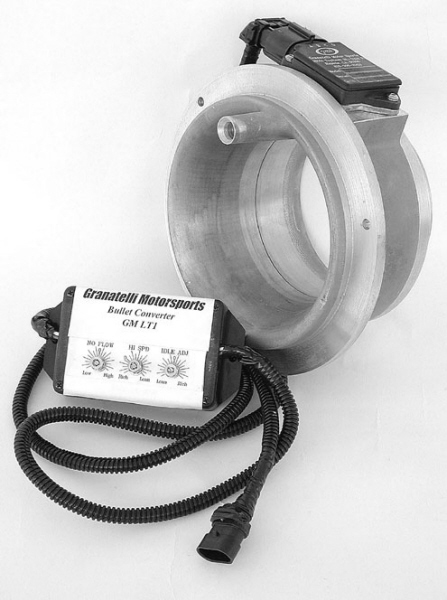
p76770_image_large.jpg [ 90.49 KiB | Viewed 6096 times ]
|
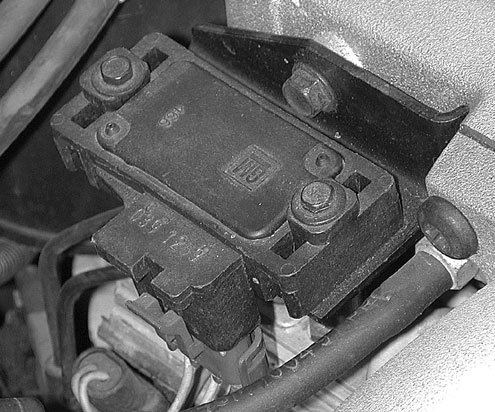
map sensor.jpg [ 60.6 KiB | Viewed 6095 times ]
|
_________________ ex: Alfa Romeo 156 2.0 TS
|